FieldLogs - An Overview
FieldLogs is a powerful digitalization platform that makes workflows more efficient and streamlines business processes. It offers an end-to-end solution that allows businesses to automate complex processes, quickly respond to changing regulations, and remain compliant.
FieldLogs leverages mobile and digital technology, enabling users to capture data quickly and accurately while providing real-time visibility into operations. By providing businesses with this data, FieldLogs offers opportunities to make informed decisions based on trends, improve performance, and maximize the value of their operations.
FieldLogs also offers businesses the ability to continually remain in service while following complex procedures and staying up-to-date with changing regulations.
It is a key part of the E2E solution of several big players in diverse sectors - Aviation, Robotics, Logistics, Oil & Gas, etc.
FieldLogs is a powerful tool used by major commercial aviation companies for different services to streamline their engine and maintenance services. It enables companies to track and monitor their services in real-time, allowing them to make informed decisions quickly and easily. It ensures that the engine and maintenance services are up-to-date and running smoothly.
Engine Services
Aviation service provider companies offer services pertaining to engine overhaul. Different aircraft engines are maintained, each requiring customized engine overhaul services.
FieldLogs is used as part of the digitalization solution by such engine maintenance providers.
Maintenance Services
Airworthiness is the measure of the suitability of an aircraft for a safe flight. It comprises the quality check of various components of the aircraft and its structure. A certificate of airworthiness is initially issued by the local governing aviation authority and is maintained by performing mandatory regular maintenance checks.
Aircraft maintenance is the performance of these maintenance checks on every aircraft in service. It is intensely regulated and includes regular preventive servicing, overhaul, inspection, replacement, testing, compliance with airworthiness directives and repair activities by certified Maintenance, Repair and Overhaul (MRO) technicians.
Line Maintenance includes all maintenance that is carried out before a flight to ensure the airworthiness of the aircraft. It includes troubleshooting, required defect rectification, and replacement of components.
Base Maintenance is carried out in an aircraft hangar in an airport. It covers a series of checks and MRO activities. Base maintenance is aircraft-specific. Airlines use different maintenance schedules and procedures that are specific to their aircraft.
These maintenance operations also include the various components of the aircraft, which are manufactured by different Original Equipment Manufacturers (OEMs) aviation companies.
Traditionally, these maintenance workflows were paper-intensive. The paper trail for repairs was usually long, time-consuming , and complicated. Inadvertent manual errors were very expensive in terms of time and effort.
Further, the aviation and aerospace industry constantly faces unique regulatory requirements and work business processes that they must support. Their digitization operation is further complicated by how OEMs provide content, that is injected into their operations.
The aircraft maintenance industry has benefitted greatly from the creation of Electronic Task Cards. Electronic task cards have streamlined the entire process, improving transparency and data sharing. They are easy to access, read, and modify on the shop floor using mobile devices, saving time and effort.
The FieldLogs Solution
FieldLogs is a powerful Electronic Task Cards Operation System, that can be used to track and document job progress, schedule Sub-tasks, record inspection signatures and send notifications when the job is completed.
FieldLogs also has an effective Manual Catalog Management System, which streamlines the process of digitizing new OEM manuals and manages revisions for existing content and manuals.
FieldLogs creates Task Cards or Templates from the OEM Manuals. These Templates can be used to generate Tasks that are assigned to technicians on the shop floor. FieldLogs has a complete Task Cards Operations Management System that enables collaboration between various stakeholders, approval processes, data sharing, reporting, and various other supporting functions.
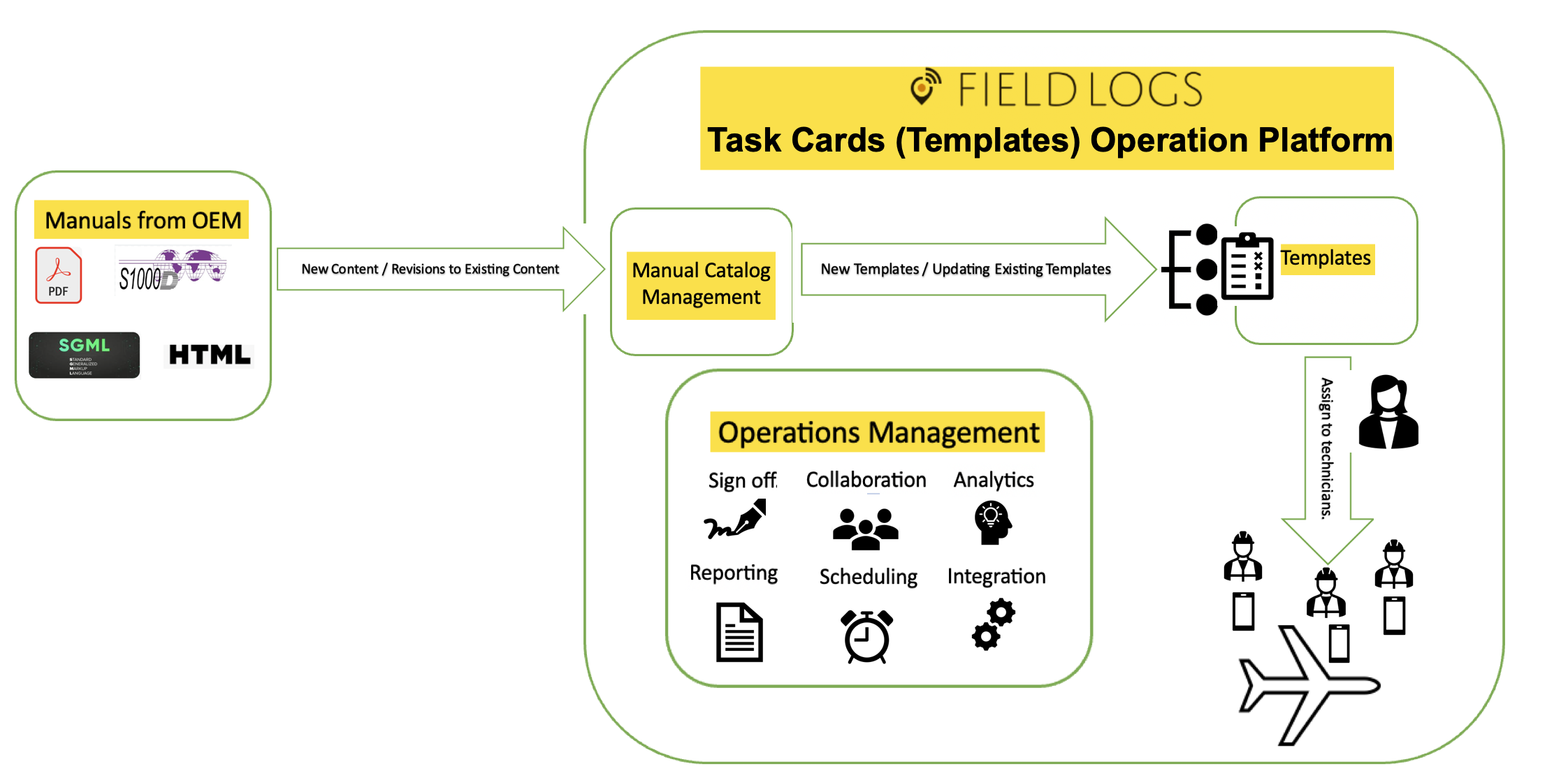
Note
Task Cards also referred to as Templates, are an integral part of the FieldLogs platform.
A Template is designed to contain step-by-step instructions to perform a particular task. It can also capture user input pertaining to the task.
Once a Template is created, Tasks can be created from it, to be executed on the shop floor. Templates provide the structure and guidance needed to complete tasks in a consistent and efficient manner.
FieldLogs is used by major e-commerce retailers as part of their warehouse management solution. These warehouses have order-picking systems in which mobile robots are used. Although there are humans involved in order fulfillment, these warehouses are largely operated by different kinds of robots.
![]() |
Image Source: www.waredock.com
These mobile robots carry the shelves (referred to as inventory pods) to employees in a pick station.
![]() |
Image Source: www.waredock.com
In pick stations, employees pick the items required for the customer order from the inventory pods and put them in the order pod. This then moves to shipping after fulfilling all orders.
![]() |
Image Source: www.waredock.com
In such a robotic mobile fulfillment center, repetitive and non-value-adding tasks such as walking to reach storage locations are done by robots, freeing up employee time and enabling them to focus on more important work.
Tote boxes with the customer orders are put on a pallet for shipping. The palletizer robot stacks totes on the pallet when they leave the facility. The depalletizer robot takes them off the pallet and places them on conveyors when they enter a facility.
![]() |
To fulfill customer orders, each robot needs to complete a sequence of work instructions and each work instruction includes a set of retrieval requests.
FieldLogs is used extensively and exclusively in deploying the many automated systems that allow a robot centered warehouse to function. FieldLogs also guides the construction and installation of the safety measures in these facilities. The specific areas FieldLogs is utilized in are listed below::
1. Deployment of Robotic Systems:
The deployment of robots in a warehouse facility is a highly complex mission involving several steps. It involves a wide range of tasks including floor considerations, path planning, and safety considerations. Optimal positioning of chargers, packing machines, robotic arm stations, and related support and safety systems is done based on the parameters of the individual facility floor.
FieldLogs Task cards are used to carry out the steps involved in such installations. A sample FieldLogs Task involved in installation is shown below:
![]() |
2. Installation of safety systems:
The warehouse robots perform repetitive and hazardous tasks including moving heavy materials, parts, tools, and specialized devices. Safety considerations are required to safeguard employees and equipment.
A variety of safety systems like enclosures on the plant floor, partitions for storage, robot safety fencing, and conveyor perimeter guarding may be required. Safety auditing of the floors is done to demonstrate compliance with regulatory standards.
FieldLogs Task cards are used to carry out the steps involved in the installation of such safety systems.
3. Quality Inspections:
Quality Inspections are carried out on the order fulfillment tasks.
For example, an organization may take a random sample of 20% of the tasks to check if the tasks are completed to the required standard. To cover 20% of the tasks, one in every five tasks is considered by the system. The criteria for the quality check could be a wide variety or combination of parameters. FieldLogs offers the flexibility to configure any required criteria and respond to them.
When five tasks are completed, one of them is picked at random for the quality check. This is repeated for every five tasks until all the tasks are completed by the system. The metrics are then generated.
To implement this solution, FieldLogs Operation Plans are used. The Operation Plan triggers a quality inspection task for every fifth task completed. Time-based and event-based triggers can be used to carry out required tasks.
4. Planning and Scheduling:
FieldLogs can be used to plan and schedule tasks. This capability is used as part of the warehouse management system. Reports and charts can be generated as required.
A sample Gantt chart of the progress of work is shown below.
![]() |
Logistics companies use FieldLogs as part of their operations planning solution.
The below infographic gives an overview of how FieldLogs features enable the operations planning process of a logistics company.
![]() |
As seen above, FieldLogs is used extensively by logistics companies in several key areas. These are discussed in detail below.
Introducing new technology to a workspace involves several steps. A custom Template can be utilized to create tasks to ensure that machinery is installed and configured correctly.
The custom Template contains instructions. These instructions form the steps of the Template. These steps may contain response fields, which capture user input, Checkboxes, Free text fields, Tables, Forms, etc. can be used to allow the installation technicians to record data. These steps provide a structure to ensure that the job is done to the same standard every time, according to the guidelines of the work instructions.
Supervisors and managers can know the current status of installation tasks and monitor progress at any stage by just looking at FieldLogs. FieldLogs gives them important information, like the following:
Has the machinery been completely installed?
Was the installation process successful?
If not, what were the issues encountered? (Issues can be raised as Flags)
Details regarding the technician's role in the installation
Resource usage (parts, tools, and consumables)
Whenever a piece of machinery needs to be updated to a newer version, the original Template that was created for the earlier version can be easily revised to cater to the new version.
With FieldLogs, user permissions can be configured to ensure that only qualified and authorized personnel are handling the installation tasks.
If there are any OEM (Original Equipment Manufacturer) documents detailing processes, they can be easily converted into FieldLogs Templates and can be used to create Tasks to make the installation process easier.
FieldLogs Operation Plans allow for scheduled Task creation, which can be customized to the required frequency and specify the templates that need to be used.
This feature is used in scheduled maintenance checks to ensure that technology is being properly maintained and employees are following company procedures.
If it is required that operations must resume only after every piece of technology has been checked to be working properly, suitable event triggers can be configured. Operation Plans based on these triggers can be used to ensure that normal operations tasks cannot be assigned until all the maintenance tasks have been completed.
If maintenance operations are outsourced to a third party, FieldLogs user permissions can be used to provide access to only the tasks pertinent to them and exclude them from everything else.
If an issue is raised during operations or maintenance, management will be able to know immediately, and Tasks based on Templates that perform appropriate corrective actions can be run.
Templates provide a consistent process for products that employees can easily access.
Quality control tasks can be implemented to ensure that all products being shipped, meet company standards. If defective products are regularly being produced, management will be able to track down the issues by looking into Fieldlogs and performing maintenance checkups.
Tasks to check production and demand sign-off can be implemented in order to ensure that the quality of products and processes is up to company standards.